TRL-8
Fluxes:
- AN-69 environmentally friendly molten flux for surfacing low-, medium- and high-alloyed steels (TU U 24.6-05416923-096:2008)
- ANK-45 environmentally friendly agglomerated flux for surfacing low-, medium- and high-alloyed steels (TU U 24.6-05416923-095:2008)
- AN-44 environmentally friendly molten flux for welding low-carbon and low-alloy steels
- ANK-73 environmentally friendly agglomerated flux for surfacing (TU U 24.6-05416923-101:2011)
Market and economic attractiveness
- Currently, there are no similar molten fluxes for surfacing in Ukraine.
- There are no surfacing fluxes in the world with similar welding and technological properties that do not contain fluorine compounds (AN-69, AN-44).
- The main advantage of this agglomerated flux is the low production cost compared to fused fluxes (ANK-45, ANK-73).
The main advantages (strengths) of the development
- The flux guarantees the separation of the slag crust from the surface of the deposited layer, including at elevated temperatures (up to 5500 C), excellent formation of the weld metal, increased stability of the existence of the arc discharge, and the absence of the release of environmentally harmful fluorine compounds (in the absence of the latter in the flux cored wire) – AN -69.
- The flux guarantees the separation of the slag crust from the surface of the deposited layer, including at elevated temperatures (up to 5500 C), excellent formation of the weld metal, increased stability of the existence of the arc discharge – ANK-45.
- The resistance of flux grains to destruction (95%) and sorption (0.115…0.117%) of moisture is at the level of fused pumice fluxes – ANK-45.
- Ensures the absence of release of environmentally harmful fluorine compounds (in the absence of the latter in the flux cored wire) – ANK-45, ANK-73.
- The flux guarantees the separation of the slag crust from the surface of the metal of the seam, including when welding in a narrow development – AN-44.
- Provides a guaranteed penetration, excellent weld metal formation, increased stability of the existence of an arc discharge, and the absence of the release of environmentally harmful fluorine and manganese compounds (in the absence of the latter in the flux-cored wire).
Main characteristics
Basicity of the flux according to:
The formulas of the International Institute of Welding are compiled | 0.75…0.8 (AN-69, ANK-45) 1.0-1.1 (AN-44) |
Oxygen ion activity (the main metallurgical characteristic of fluxes) | 0.45…0.5 (AN-69, ANK-45) 0.085-0.09 (AN-44) |
When using conventional welding wires, the oxygen content in the weld metal | does not exceed 0.05%, phosphorus 0.035%, sulfur – about 0.01% (AN-69, ANK-45) |
When using AP-AN8f profiled wire, the content of phosphorus and sulfur is found | within 0.02% (AN-44) |
- When using high-carbon wires, the sulfur content is reduced to 0.002%, which guarantees the absence of hot and salty cracks in the deposited layer (AN-69, ANK-45).
- The level of separation of the slag crust is at the maximum mark (AN-69, ANK-45).
- When using standard wires for surfacing low-, medium-, and high-alloyed steels, the fluoride -free flux ensures minimal susceptibility of the metal to hydrogen porosity (at the level of general-purpose fluxes) – AN-69, ANK-45.
- The level of separation of the slag crust is at the maximum mark (АН-44).
- The flux is intended for electric arc welding of structures, parts and assemblies of machines operating in all climatic conditions, providing a welded layer of metal resistant to intensive wear, including abrasive and shock loads at high specific pressures (ANK-73).
Ready state
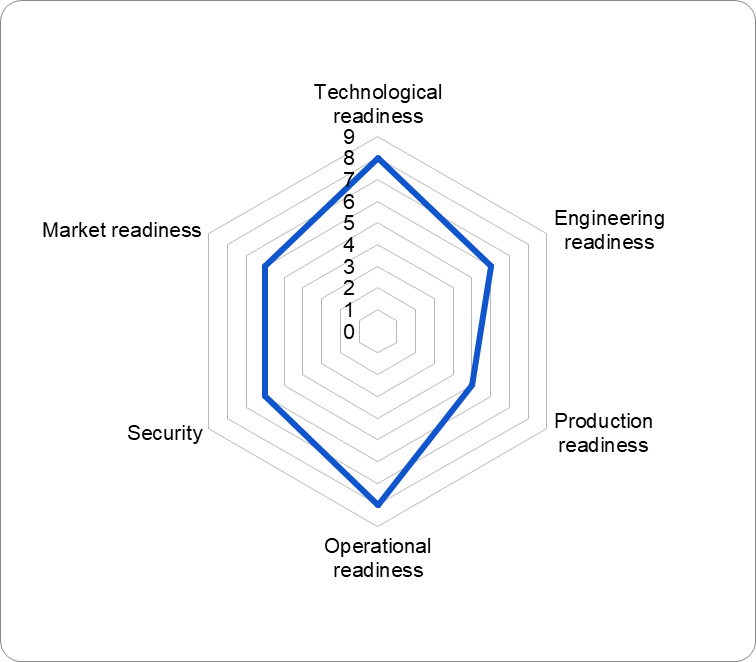
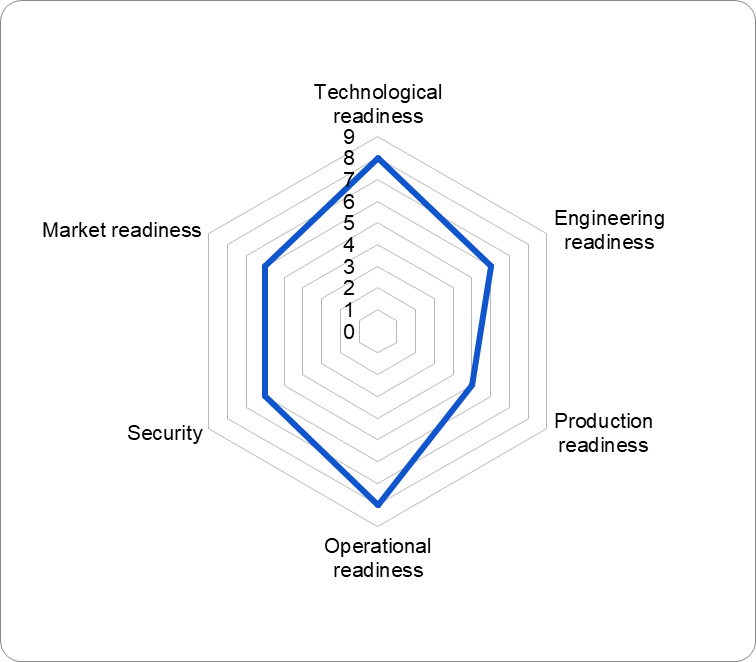
- The product is integrated into the system and tested
- Production on the experimental line has been carried out
- Production in real conditions has been carried out
- Organizational preparation of production and service has been completed
- Patent applications have been submitted
- Product certification received
Information about developers
What is needed to promote development
Customers